The Basics of Thermoformed Vacuum Plastic Parts: A Beginner’s Guide
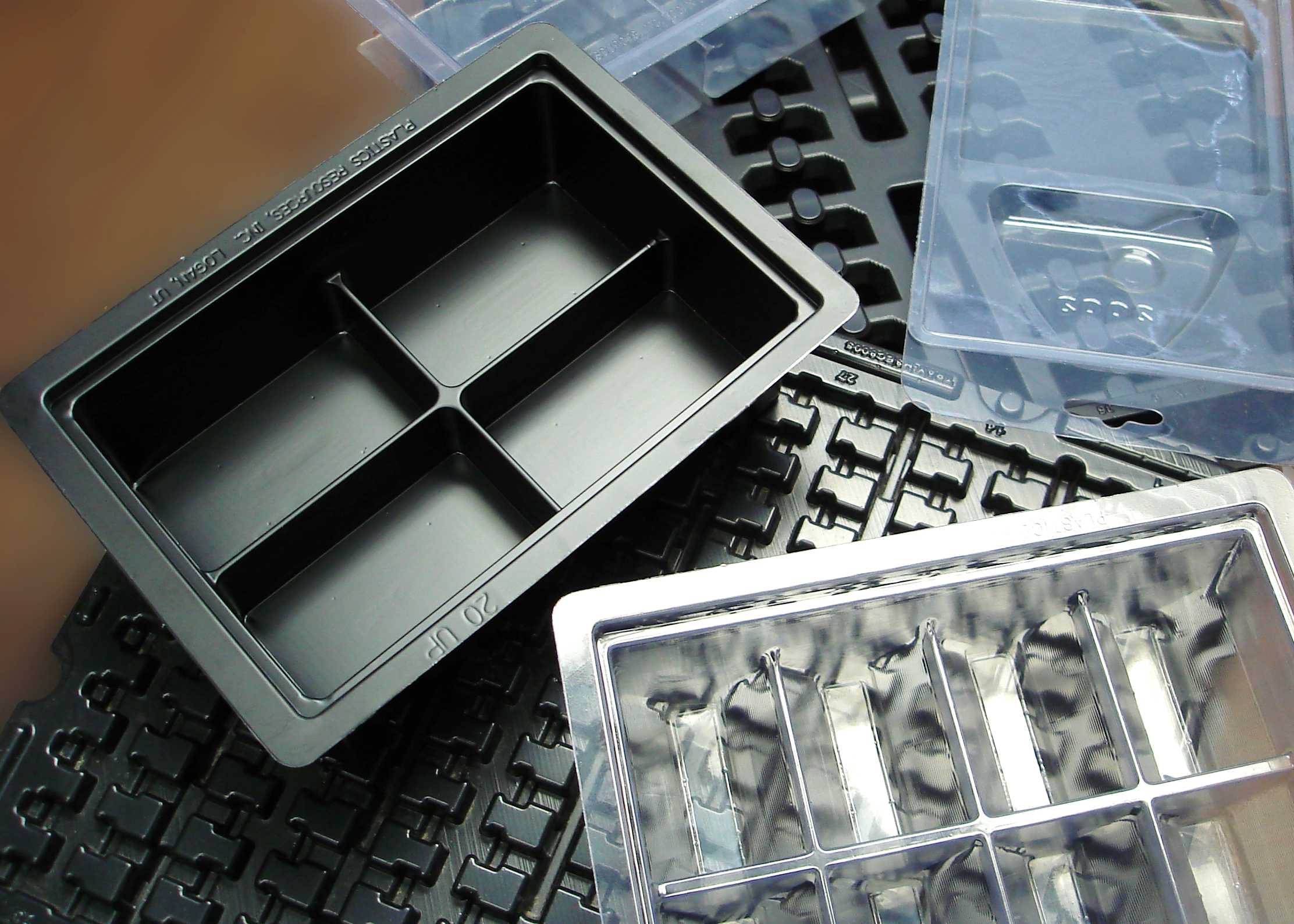
Thermoformed vacuum plastic parts might sound like a complex topic, but once you get the basics, it’s quite fascinating. These parts are all around us, from packaging to automotive components. Understanding how they’re made and their applications can give you a new appreciation for everyday items. Let’s dive into the world of thermoforming and vacuum forming to see what it’s all about.
What is Thermoforming?
Thermoforming is a manufacturing process where a plastic sheet is heated to a pliable forming temperature, shaped into a specific form, and then trimmed to create a usable product. It’s a versatile method used to produce a wide range of vacuum forming china items, from disposable cups to heavy-duty industrial components. The process involves different techniques, including vacuum forming, pressure forming, and twin-sheet forming.
Understanding Vacuum Forming
Vacuum forming, a subset of thermoforming, involves heating a plastic sheet until it becomes flexible and then using a vacuum to draw the sheet over a mold. This process is particularly popular because it’s straightforward and cost-effective, especially for producing large parts in smaller quantities. Unlike pressure forming, which uses compressed air to form the plastic, vacuum forming relies solely on the vacuum’s suction to shape the material.
Materials Used in Thermoforming
The choice of material is crucial in thermoforming. Common plastics include ABS (Acrylonitrile Butadiene Styrene), PVC (Polyvinyl Chloride), PET (Polyethylene Terephthalate), and HDPE (High-Density Polyethylene). These materials are selected based on their flexibility, durability, and suitability for the intended application. Ideal thermoforming materials should be easy to mold, robust, and cost-effective.
The Thermoforming Process
Thermoforming involves several key steps:
- Heating the Plastic Sheet: The plastic is heated in an oven until it reaches a pliable state.
- Forming the Shape: The heated sheet custom plastic thermoforming companies is placed over a mold, and a vacuum pulls the plastic tightly against it, forming the desired shape.
- Cooling and Trimming: Once the plastic cools and hardens, it’s removed from the mold and trimmed to the final dimensions.
Design Considerations
Good design is vital in thermoforming. Factors like material thickness, mold design, and cooling time all influence the final product’s quality. To ensure efficient production, it’s essential to account for the plastic’s shrinkage and the mold’s intricacies. Simple, functional designs often yield the best results.
Mold Types and Their Role
Molds are the heart of the thermoforming process. They can be made from various materials, including wood, aluminum, and epoxy, each offering different benefits. The choice of mold material affects the cost, production speed, and precision of the final product. Aluminum molds, for instance, are durable and provide excellent detail, making them suitable for high-volume production.
Advantages of Vacuum Formed Parts
Vacuum forming offers numerous advantages. It’s cost-effective, especially for low to medium production volumes, and allows for rapid prototyping. The process is also versatile, accommodating a wide range of sizes and designs, making it ideal for custom applications.
Limitations of Thermoforming
Despite its benefits, thermoforming has limitations. It’s not suitable for producing highly detailed or extremely thin parts. Additionally, the process can result in material waste, although this can be mitigated through recycling. Designing for thermoforming requires careful planning to avoid issues like webbing or inconsistent thickness.
Applications of Thermoformed Parts
Thermoformed parts are used across various industries. In packaging, they create lightweight, protective containers. The automotive sector uses them for interior components and protective housings. Even in the medical field, thermoformed plastics are used for equipment covers and trays. This versatility highlights the importance of thermoforming in modern manufacturing.
Quality Control in Thermoforming
Maintaining high quality in thermoforming involves rigorous testing and inspection. Techniques such as visual inspections, dimensional measurements, and material testing ensure that the final products meet the required standards. Consistent quality control helps in reducing defects and improving overall efficiency.
Sustainability and Recycling
With growing environmental concerns, the sustainability of thermoformed plastics is crucial. Many thermoforming materials are recyclable, and manufacturers are increasingly focusing on using recycled plastics. This not only reduces waste but also lowers production costs and environmental impact.
Future Trends in Thermoforming
The future of thermoforming looks promising with technological advancements driving innovation. Improved automation and new materials are making the process more efficient and sustainable. Emerging applications, such as in the aerospace and renewable energy sectors, are expanding the possibilities for thermoformed parts.
Conclusion
Understanding the basics of thermoformed vacuum plastic parts opens up a world of possibilities in manufacturing. From simple packaging solutions to complex automotive components, this versatile process plays a crucial role in various industries. As technology evolves, thermoforming will continue to adapt, offering new opportunities and applications.
FAQs
- What is the difference between thermoforming and injection molding?
- Thermoforming involves heating and shaping a plastic sheet over a mold, while injection molding injects molten plastic into a mold cavity.
- How durable are thermoformed plastic parts?
- The durability depends on the material used and the application, but generally, thermoformed parts are strong and resilient.
- Can thermoformed parts be recycled?
- Yes, many thermoformed plastics are recyclable, making them a sustainable choice for various applications.
- What industries use vacuum-formed parts the most?
- Industries like packaging, automotive, medical, and consumer goods frequently use vacuum-formed parts.
- How do I get started with designing thermoformed parts?
- Begin by understanding the material properties, design for manufacturability, and collaborate with experienced mold makers to ensure efficient production.